Best Practices for
Managing Inventory at Remote Project Sites
Keeping good inventory records is essential for project site operations.
It helps to ensure that the right materials are available when needed, which can help to prevent delays and downtime. It also helps to ensure that the materials are being used efficiently and that there is no waste.
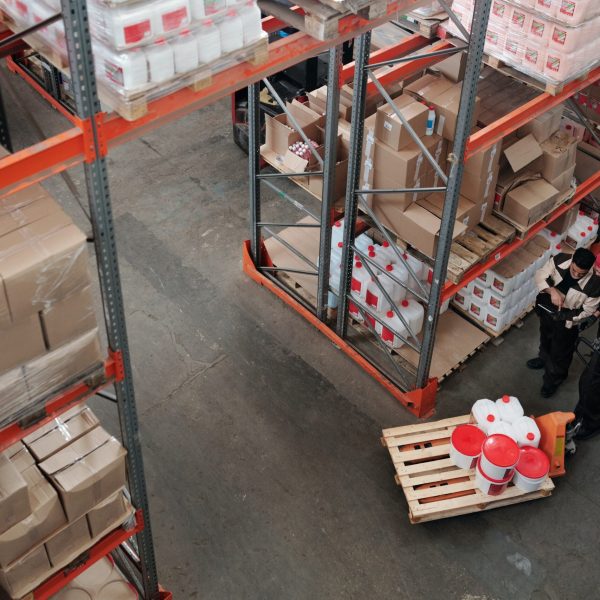
Another challenge is operational efficiency. When materials are not available when needed, it can cause delays and reduce productivity. By keeping good inventory records, you can ensure that the right materials are available when needed, which can help to improve operational efficiency. For example, you can use a reorder point system to determine the optimal level of inventory for each item and order more supplies when the inventory falls below that level.
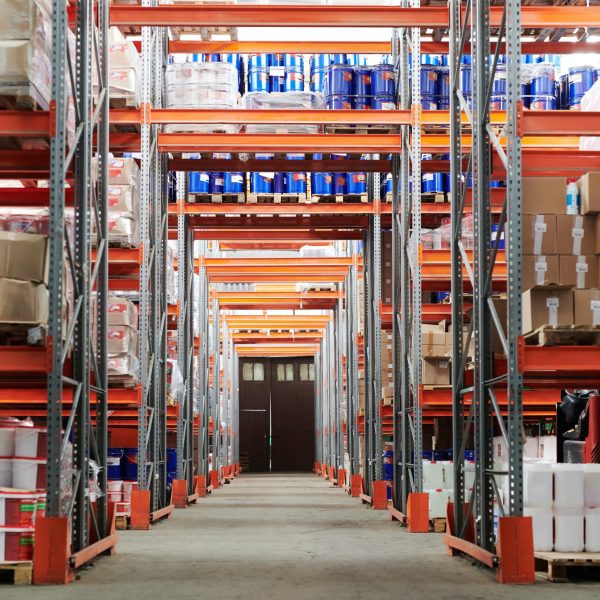
Equipment uptime is also critical for project site operations. When equipment breaks down, it can cause costly delays and reduce productivity. By keeping good inventory records, you can ensure that all the parts required to keep equipment properly maintained are always available and that there is no unplanned downtime. For example, you can use a preventive maintenance schedule to plan the maintenance activities for each equipment and check for the availability of the parts long before the scheduled date to perform the maintenance.
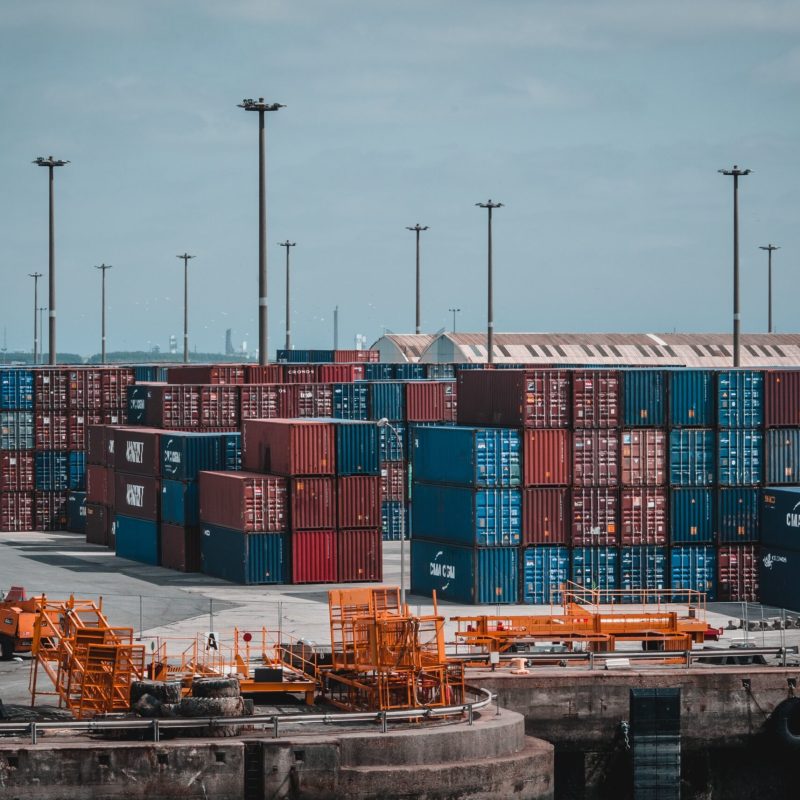
Some common best practices for remote project site inventory management include:
Strict access controls, with 24-hour monitoring of additions and removals.